Overview
There are two types of mine designs for mineral mining: surface (open pit) and underground.
Surface
Surface mines are generally preferred if the ore body is relatively shallow and uniform, and are made by digging into the Earth’s surface one layer at a time. The final mine is cone-shaped.
First, we drill holes in the ground and fill them with explosive. After the rock has been broken up by blasting, it is loaded into giant haul trucks using large shovels and front-end loaders. Rock containing gold, copper and other valuable minerals is hauled away for processing and waste rock is taken to a separate area for storage. Areas of waste rock are later rehabilitated.
As we dig farther down, it is necessary to dewater the mine to ensure that the water level remains below the pit floor. Each day, we pump thousands of gallons of water from the pit. Much of it is reused on-site (to control dust, etc.). Excess water is treated and discharged back into nearby rivers or lakes.
A significant amount of monitoring takes place in and around the open pit, to keep a watchful eye on:
- Slope stability and dewatering-induced settlement
- Noise, dust and vibration
- Water levels and water quality, including pit wall run-off and groundwater
Underground
Underground mines are used to extract minerals or metals from deep in the Earth. When building an underground mine, we dig a tunnel to get to the minerals. This can be a straight vertical tunnel called a shaft or a tunnel that spirals gradually downwards, called a decline. To access the ore from the shaft or decline, we dig other tunnels. We also mine out tunnels to provide proper ventilation and emergency exits.
We mine the tunnels and the ore bodies by drilling and blasting. The broken-up ore is then transported to the surface for processing. Waste rock may be transported to the surface or left in the mine and used to fill empty space.
Once we remove all material from inside the tunnels, we support them to make them safe. The type of ground support needed depends on how stable the ground is and how long the tunnel is going to be used for. These factors are identified in advance so that engineers can design the mine for maximum safety and value.
Ground support may be provided by rock bolts or split sets, which are forced into drilled holes to exert pressure on the surrounding rock, which keeps it intact. Chemicals or grouts are sometimes added with rock bolts to give them greater strength. We also install wire mesh to keep smaller rocks from falling down.
High-pressure spraying of Shotcrete (a mortar/concrete mix) onto the tunnels’ walls and backs provides more support. As we complete mining in each stope, we backfill it with a cement mixture as well.
Underground mines pose a greater safety risk and limit the size of equipment that can be used; however, they cause less environmental disturbance.
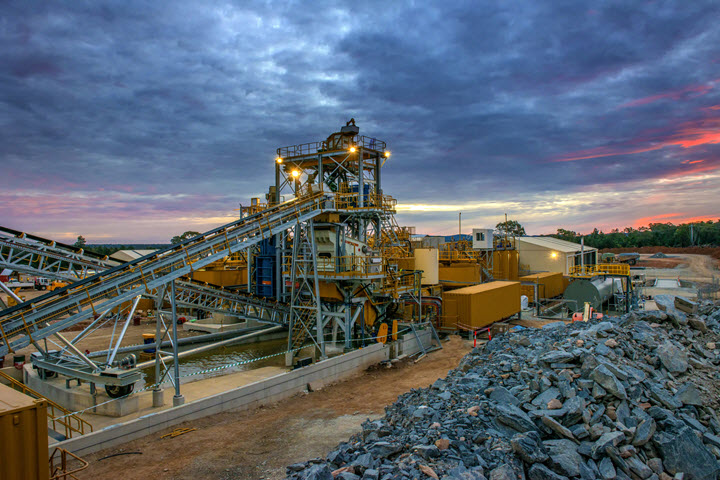
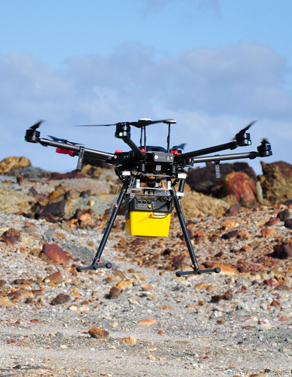
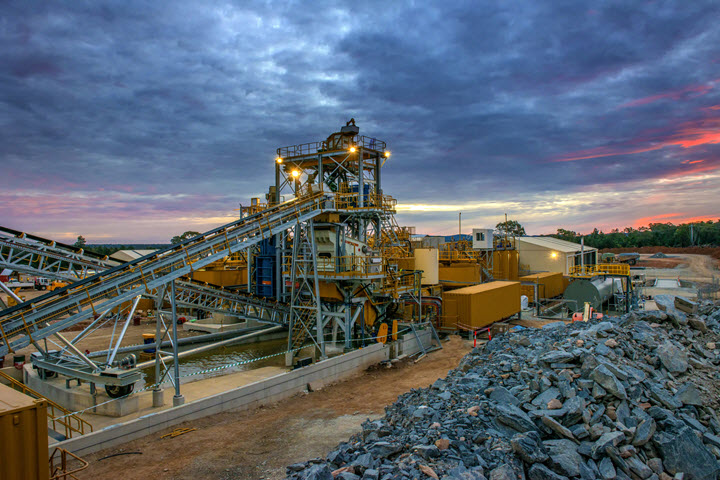